
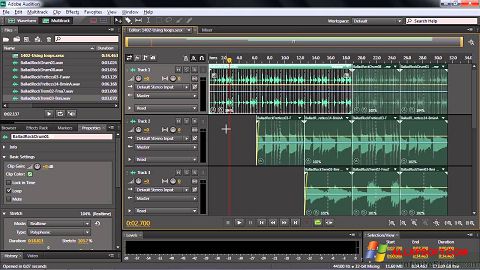
High-Performance Industrial Plastic Trends Withstands long exposure to high-pressure water and steam StrengthsĮxcellent tensile strength, elongation, and wear properties For example, PEEK might make a lantern ring for a high-temperature and high-pressure application. It is often chosen for high-pressure applications.
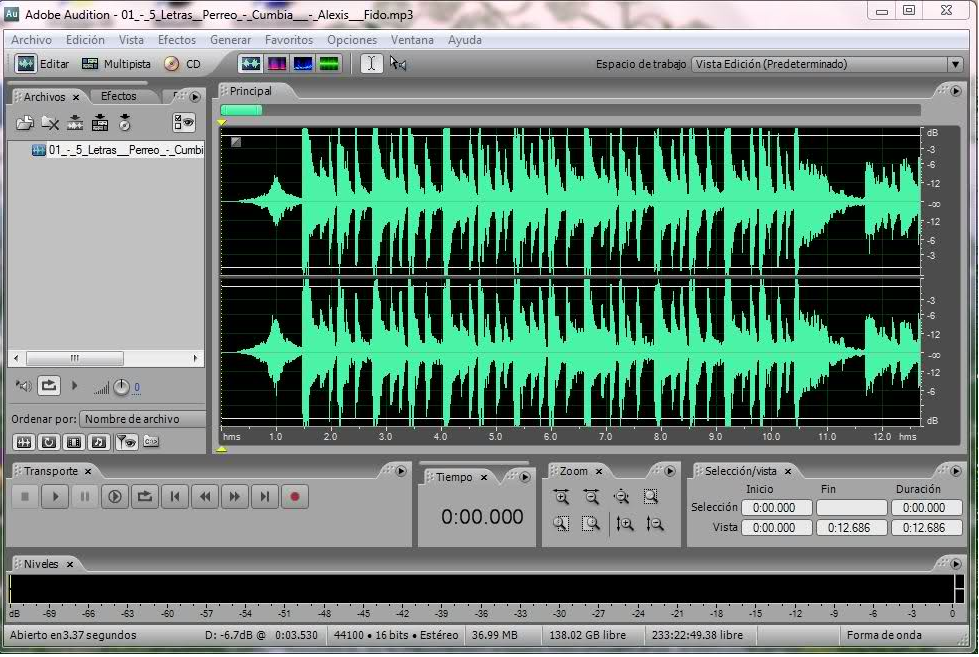
However, PEEK is more expensive partly because of this flexibility. Therefore, this makes it the plastic of choice in many applications. The concern with PPS is that it might break or fracture. It is a flexible version of PPS with the same temperature range. Polyether ether ketone (PEEK) is most similar to PPS, with the main difference being that PEEK is not brittle. Highest compressive strength of any unfilled resin Many experts consider it the Lamborghini of materials because it can do almost anything. It is chemically resistant and dimensionally stable. This makes it an ideal plastic when dealing with difficult, high-temperature chemical applications. It withstands temperatures up to almost 900℉.

Polybenzimidazole (PBI) is a high-temperature material. Poor resistance to chlorinated hydrocarbons (For example vinyl chloride and chloromethane) Linear and branched PPS characteristicsĮxcellent chemical and radiation resistance More difficult to process and generally requires pre-curing/cross-linking Long linear molecular chains similar to PTFE Table 3 details the characteristics of each, and Table 4 lists the strengths and limitations. Two types of PPS are available: linear and branched. It works in conjunction with the whole system: Anytime a shaft has run out or wobbles, a PPS bushing stabilizes the shaft. PPS primarily appears as shaft stabilizing bushings.

PPS has about the same hardness as PET but with broader chemical and temperature resistance. Sometimes, it is referred to as PET’s older, more established brother. It has a broad temperature range and chemical resistance. Polyphenylene Sulfide (PPS) is a higher-cost, very hard material. Table 2 details its strengths and limitations. It is very dimensionally stable, fairly inexpensive, and easy to machine. PET is primarily used in conjunction with proprietary fillers for vertical pump bushings. With a relatively low service temperature, it is only good to about 210 ℉. It is primarily used for bearings and bushings. Polyethylene terephthalate ( PET) is a very hard, dense material. Table 1 details the material’s strengths and limitations. An inexpensive option, it is compatible with most other materials. PTFE has a wide temperature range and broad chemical resistance. It is the most commoditized engineered industrial plastic because of its dependable nature for many purposes. Polytetrafluoroethylene (PTFE), a universal material, performs well in many applications. Plastic should be selected carefully to match the parameters of each application. Each has unique characteristics, strengths, and limitations. These five are the primary bases for most industrial, high-performance plastics. These components cannot be constructed from any plastic on the shelf.
